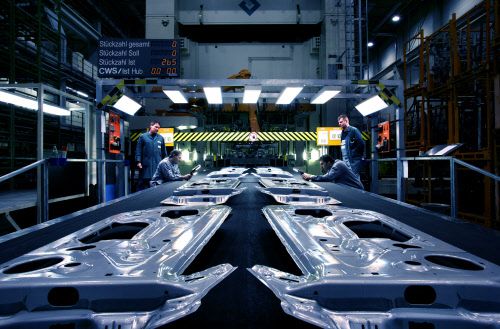
Fertigung von Automobil Komponenten am Standort Schwäbisch Gmünd. Mit Hochöfen und verrußten Hallen haben die Stahlspezialisten in Deutschland nichts am Hut. Der aus Linz gelieferte Rohstoff wird hier geformt.
Schwäbisch Gmünd – Peter Schwab ist offensichtlich Techniker aus Leidenschaft. Der Österreicher erklärt mit Gesten und Worten zum wiederholten Mal, was man im Voestalpine-Werk in Schwäbisch Gmünd kann, was andere nicht können. Fest presst der 51-Jährige vor einer nagelneuen Produktionslinie, vor der ein knalloranger Roboter thront, seine Faust in die geöffnete Hand. "Wenn das nicht passt, kommen Sie nicht mit einem kleinen Gummihammer aus." Was der Voestalpine-Vorstand sagen will: Am Ende dieses Fertigungsprozesses kommt ein Bauteil heraus, der sich in die Karosserie eines Autos präzise einpassen lässt.
Es handelt sich um sicherheitsrelevante Teile, die nun von der neuen Anlage laufen sollen, in die Voestalpine elf Millionen Euro investiert hat. Leichtbaukomponenten aus Spezialstahl konnte man an diesem Standort in Süddeutschland, an dem mit rund 630 Mitarbeitern jährlich 150 Millionen Euro umgesetzt werden, auch bisher schon herstellen.
Stahl ist nicht gleich Stahl
21 Millionen Teile, die unter anderem dafür sorgen, dass ein Auto auch bei einem Crash nicht vollständig zum Blechsalat wird, werden hier schon jetzt jährlich am Kompetenzzentrum für "Warmumformung" produziert. Es sind dies etwa die Säulen zwischen Vorder- und Hintertür oder Streben in Seitenwänden und Türen. Rostfrei sind sie und "fünfmal härter als ein Messer": Voestalpine-Chef Wolfgang Eder unterbricht seinen begeisterten Divisionschef für die Stahlverarbeitungssparte Metal Forming Division, um noch einmal vor Augen zu führen, dass Stahl nicht gleich Stahl ist. Der Grund, warum nicht nur Journalisten, sondern auch Kunden aus nah und fern, lokale Prominenz und Mitarbeiter geladen sind und das Catering vom Konzernstandort Linz samt Küche, Gerätschaft und Personal extra angereist ist, um sie zu bekochen: Man feiere eine technische Revolution, so die Voest-Menschen.
Die neue Anlage könne etwas, "wovon es lange geheißen hat, dass es physikalisch unmöglich sei", sagt Schwab. Genau genommen werden nun feuerverzinkte Stähle in einem einzigen Arbeitsschritt zu höchstfesten, pressgehärteten Stählen – phs-direct heißt das Verfahren – umgeformt. Möglich wurde dies, weil man nach 15-jähriger Forschungs- und Entwicklungszeit in der Lage ist, den Prozess der Verformung effizienter umzusetzen. Beim bisherigen Verfahren wird der Stahlteil durch den Ofen, der ihn auf 900 Grad erhitzt, geschickt. Nun werden die Bauteile in einem Prozessschritt erhitzt, geformt und gehärtet. Der Schutz aus Zink soll das Rosten bei kleinen Kratzern verhindern.
Diese Art von Bauteilen ist noch so neu, dass man erst mit möglichen Abnehmern in Verhandlung ist. Viele von ihnen haben Standorte nicht weit entfernt von dem beschaulichen Städtchen mit den schmucken Fachwerkhäusern und der Region, die sich zu einer Art Mekka der Autozulieferer entwickelt hat. Bosch, die Magna-Steyr-Tochter Erhard & Söhne und andere beliefern von hier aus die deutschen Autobauer Daimler, Audi oder Porsche. Einer der ersten Bauteile wurde im Porsche Panamera verbaut.
Schauen auf den Preis
Der Vorgängerprozess wird mittlerweile lizenziert. Mit der neuen Anlage wollen die Linzer beweisen, dass die Serienproduktion funktioniert. Ob die Rechnung wirtschaftlich aufgeht, muss sich weisen. "Interessant ist das schon", sagt ein Audi-Mitarbeiter: "Aber auch die Konkurrenz schläft nicht." Aluminium und Silizium – eine andere Mischung, als die Linzer verwenden – könnten auch etwas. Andererseits: "Wir schauen uns das an. Aber am Ende spielt auch der Preis eine Rolle."
Um den geht es naturgemäß auch Konzernchef Eder. Denn höherwertige Spezialstähle bedeuten höhere Preise. Nicht nur Premiumautobauer würden sich mittlerweile dafür interessieren, sagt Eder. Konkurrenz kommt aber zunehmend von Leichtmetall und Verbundmaterialien, die den Karosseriebau revolutionieren. Die Werkstoffe sind schon wegen ihres geringen Gewichts interessant. Hohe Kosten verhindern aber den Einsatz in der Massenproduktion.
Geht es nach Eder, bleibt die Zukunft deswegen für Stahl noch lange erquicklich: "Die Nachfrage wird gerade wegen E-Mobilität und leichter werdender Autos noch steigen.(Regina Bruckner, 12.7.2016)