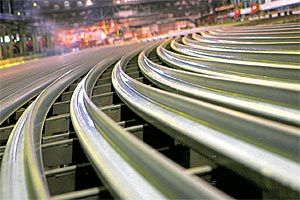
Fester, härter, länger: Bis zu 120 Meter lang sind die Hightech-Schienen, die im Voestalpine-Werk in Donawitz vom Band rollen.
Wie ein schnaubender Walfisch liegt das langgezogene Schienenwalzwerk der Hütte Donawitz in der schmalen Mur-Mürz-Furche im Herzen der Steiermark. Im Inneren seines Bauches, in verrußten Hallen voller riesenhafter Maschinen, glüht und zischt und dampft es nur so. Auf der einen Seite des Werks schweben matte Stahlquader per Magnetkran herein, wo sie wenig später von einem Ofen verschluckt werden. Am anderen Ende gleiten schlanke Schienenstränge wieder heraus und durch den Schnee in Richtung Verladebahnhof.
Dazwischen: Überdimensionale Nudelwalker, die den Stahl zu bis zu 120 Meter langen, glühenden Marzipanschlangen auswalzen und im Dreiminutentakt auf Rollen durch die Halle schubsen. Kreiselförmige Walzen mit den verschiedensten Profilen, die sich meterhoch neben den Maschinen stapeln. Eine Armee von Greifarmen, die behutsam die geformten Schienen in ein puddinggelbes, sprudelndes Bad heben. Angesichts der geballten industriellen Kraft fühlt man sich ein wenig in eine andere Zeit oder in den Film Metropolis versetzt.
"Man glaubt nicht, wie viel Hightech in diesen Schienen steckt", verwischt Norbert Frank von der Technologieabteilung des Voestalpine-Werks Reminiszenzen an die industrielle Revolution. "Wir forschen ständig an neuen Stahlzusammensetzungen und härteren Stahlsorten."
An diesem Tag werden 100-Meter-Schienen mit der Profilbezeichnung "VIArea136RE" erzeugt, die für Brasilien bestimmt sind, wo sie Schwergewichtszügen mit einer Achslast von 40 Tonnen standhalten müssen. "Die gehören zum Besten, was es derzeit gibt", sagt Norbert Frank.
Kopfüber ins Härtebad
Damit die Schienen besonders hart und widerstandsfähig gegen Abnützung sind, hat die Voest bereits vor 20 Jahren ein Spezialverfahren ausgetüftelt: Die sogenannte feinperlitische Wärmebehandlung. Dabei wird die Schiene kopfüber in ein Härtebad getaucht, wodurch der Kopf der Schiene - also jener Teil, auf dem die Räder aufliegen - minutenschnell abgekühlt wird, wodurch ein feineres Gefüge entsteht.
"So erreichen wir die fünffache Lebensdauer", sagt Frank. "Bei Zügen mit einer Achslast von 40 Tonnen lasten auf einer Schiene 20 Tonnen - auf der Fläche eines Fingernagels." Nach jahrelanger Forschungsarbeit an dem Verfahren und zweijährigen Tests auf einer Versuchsanlage läuft seit 2009 die selbstentwickelte Produktionsanlage. Fast nichts ist hier zugekauft - nicht ohne Grund ist Donawitz als Mekka der Maschinenbauer bekannt.
Gemeinsam mit Wissenschaftern der Leobener Montanuniversität führen die Voestalpine-Forscher Materialuntersuchungen und Simulationen durch, um das Verfahren immer weiter zu verfeinern. Im Labor, auf Produktionslinien und im Praxistest werden die neuen Stähle oft jahrelang getestet, bis sie ihren Weg in die Eisenbahnnetze finden. Bevor sie das Werk verlassen, wird jede einzelne Schiene mit Laserstrahlen und Ultraschall vermessen, um die kleinsten Fehler oder Risse im Material zu entdecken.
Mit 500.000 Tonnen Stahl, die jährlich zu 10.000 Kilometern Gleisen gewalzt werden, gehört Donawitz zu den größten Schienenproduzenten Europas, geliefert wird in alle Welt. Die Wiener U-Bahn rollt darauf, genauso wie die ÖBB, Güterzüge in den USA und Australien oder die Straßenbahnen in Lissabon und Hongkong.
Knapp 40 Kilometer entfernt, in Zeltweg, werden Schienenteile aus Leoben zu Weichen verarbeitet. In der blitzblauen Halle sprühen die Funken, die Schweißgeräte verbreiten einen verbrannten Geruch, der Boden ist mit feinen Metallspänen übersät. Mit den feinen Messerplättchen der Fräsemaschinen werden die Schienen in Form gebracht, Arbeiter in Blaumännern hobeln, schrauben und klopfen.
Millimetergenaue Feinarbeit
"Die Automatisierung ist sehr schwierig bei der Weichenherstellung", sagt Rainer Oswald, Geschäftsführer des VAE-Werks in Zeltweg, eines Tochterunternehmens des Voestalpine-Konzerns. "Bei der Bearbeitung geht es um jeden Zehntelmillimeter. Da ist Feinarbeit gefragt."
Schließlich sind die Weichen enormen Belastungen ausgesetzt, wenn ein Zug von einem Gleis auf das andere wechselt - insbesondere bei Hochgeschwindigkeitszügen, die mit bis zu 350 Stundenkilometern über die Schienen rasen. "Die Weichen halten mehr Druck stand als Stahlträger in Hochhäusern", betont Oswald. Für das sogenannte Herzstück, an dem das Rad von einer auf die andere Schiene geleitet wird, kommt Hartstahl aus Manganguss zum Einsatz. Für noch mehr Härte und Festigkeit wird auf der Oberfläche Plastiksprengstoff zur Explosion gebracht. "So wird der Verschleiß später minimiert", sagt Oswald.
Jährlich bis zu 3000 Weicheneinheiten werden in Zeltweg ausgeliefert - quasi in Maßanfertigung, da die Weichen genau auf die Geometrie der Strecke abgestimmt sein müssen. Mussten die Gleise früher händisch umgestellt werden, so läuft heute alles vollautomatisch, zentral gesteuert von wenigen Stellwerken aus.
In der Montagehalle in Zeltweg werden Weichensysteme auch komplett auf Betonschwellen vormontiert, damit der Austausch möglichst fliegend vonstattengehen kann. In speziellen Hohlschwellen befinden sich hydraulische Antriebe, welche die Weiche automatisch umstellen und sicher verriegeln. Fast jeder Einzelteil dafür wird selbst hergestellt und zusammengesetzt - auch die Elektronik, etwa eingebaute Sensoren, die Alarm schlagen, wenn die Weiche beim Umstellen langsamer wird. Oder Diagnosesysteme, die signalisieren, wenn die Bremsen des darüberfahrenden Wagons zu heiß werden.
Die Weichen für den zukünftigen Bahn- und Nahverkehr scheinen gestellt - und somit auch jene für die steirische Stahlindustrie.(Karin Krichmayr /DER STANDARD, Printausgabe, 15.12.2010)